Technical features
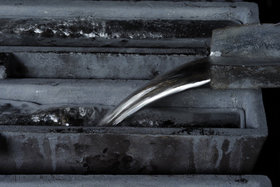
Zamak is a non-ferrous alloy with a high content of very pure zinc, combined with small percentages of aluminium, magnesium and copper (variable according to the types of use).
Zamak is the trade name originating from the initials of the four components (Z-zinc+A-Aluminium+MA-magnesium+ K-copper).
Unlike zinc, which is a fragile and low-resistant metal in its pure form, zinc alloys are characterised by extreme hardness and resistance, but also by good ductility and an excellent yield in hot-chamber die-casting applications.
The current zamak features are the result of research carried out on an international level over a span of several decades, in order to create optimal compositions for various uses and to establish allowed impurity limits.
There are three types of zamak alloys most used in die-casting processes: zamak 12, zamak 13 and zamak 15. They differ in the higher or lower copper percentage (from 0 to 3%). Besides having a fluidifying effect in die-casting, copper provides the alloy with higher hardness and resistance.
More in detail, zamak 12 (znal4cu3) offers high hardness and high tensile strength. Zamak 13 (znal4) is characterised by good dimensional stability, by a negligible decrease in impact strength in case of ageing at high temperatures and by high impact and corrosion strength.
To guarantee top-quality supplies, Effebiesse uses zamak 15, (znal4cu1), a first-choice zinc alloy offering many advantages:
tensile strength similar to zamak 12, dimensional stability, impact and corrosion strength similar to zamak 13.
ZAMAK 15 chemical composition % (according to the EN 1774 standards) |
||
Zinc |
About 94% |
|
Aluminium |
Min 3.8- max 4.2 |
|
Copper |
Min 0.7- max 1.1 |
|
Magnesium |
Min 0.035- max 0.06 |
|
Impurities |
||
Lead |
Max 0.003 |
|
Cadmium |
Max 0.003 |
|
Tin |
Max 0.001 |
|
Iron |
Max 0.02 |
|
Nickel |
Max 0.001 |
|
Silicium |
Max 0.02 |
|
Tot. Impurities |
Cd+ Pb+ Sn |
Max 0.006 |